Expert Welding Inspection Service for Security Compliance
Expert Welding Inspection Service for Security Compliance
Blog Article
Discover the Benefits of Various Kinds Of Welding Services for Your Business

In the world of industrial procedures, the choice of welding solutions plays a pivotal function in determining the high quality and performance of your company procedures. Each welding technique, from MIG to TIG, Arc, and Place welding, offers distinct advantages that provide to particular demands and needs.
MIG Welding Benefits
MIG welding, also called Gas Metal Arc Welding (GMAW), uses various advantages to businesses looking for top notch and efficient welding services. One main benefit of MIG welding is its versatility in managing numerous kinds of steels, consisting of stainless steel, aluminum, and moderate steel. This adaptability makes MIG welding a preferred choice for industries with diverse welding needs.
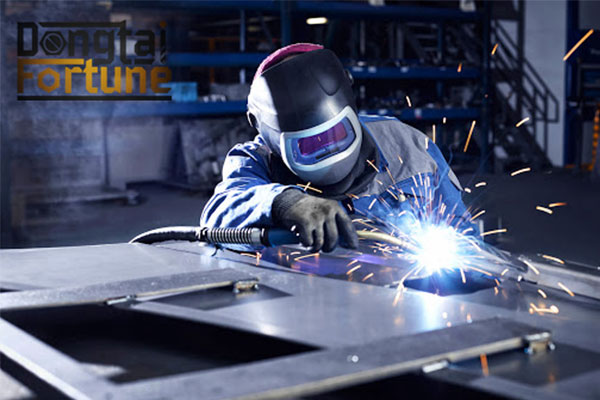
Additionally, MIG welding is a cost-effective alternative because of its reliable usage of consumables such as filler material and protecting gas. This performance equates to financial savings for companies in the lengthy run. In general, MIG welding's mix of flexibility, rate, ease of use, and cost-effectiveness makes it a recommended choice for several welding applications.
TIG Welding Benefits
Tungsten Inert Gas (TIG) welding offers exact control and remarkable top quality in welding services for services calling for high-standard and thorough welds - Welding Inspection Service. TIG welding stands apart for its capacity to produce clean and specific welds without spatter or sparks, making it optimal for applications where appearances and precision are vital. Among the key advantages of TIG welding is its convenience in welding different sorts of metals, consisting of stainless-steel, aluminum, copper, and exotic metals, supplying organizations with a flexible welding service for different tasks
Moreover, TIG welding allows welders to function with thinner products properly, as the procedure permits for reduced warmth input and much better control over the welding arc. This causes marginal distortion and a slim heat-affected zone, important for welding jobs where protecting the architectural stability of the base products is critical. In addition, TIG welding generates high-quality, visually appealing welds that frequently need very little post-weld cleanup, conserving services time and resources. Overall, the precise control, top quality welds, and flexibility make TIG welding a preferred choice for companies aiming to attain superior welding results.
Arc Welding Pros
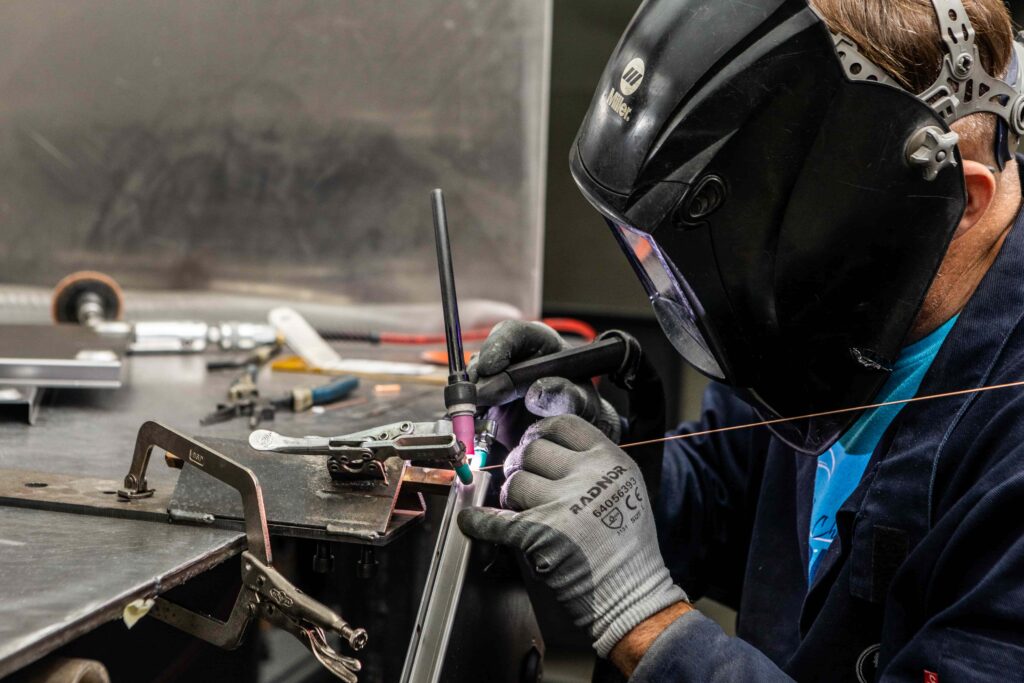
Place Welding Perks
Place welding provides countless advantages for services seeking accurate and reliable joining of steel components in their production procedures. This welding approach is highly cost-efficient because of its fast execution, marginal requirement for considerable prep work, and reduced energy usage contrasted to other welding strategies (Welding Inspection Service). Spot welding likewise provides a clean and cool coating, making it ideal for applications where looks are crucial
Among the essential advantages of place welding is its ability to develop strong and resilient bonds between metal surfaces. The procedure produces a focused heat source, resulting in a localized weld that lessens damages to the bordering areas. This focused warmth application additionally decreases the danger of bending or distortion in the bonded materials, making certain the honesty of the end product.
Additionally, place welding is very functional and can be made use of on a large range of metals and alloys, consisting of light weight aluminum, steel, and copper. Its flexibility makes it a popular choice for industries such as automobile, electronic devices, and aerospace, where precision and effectiveness are critical. Generally, the advantages of area welding make it a useful property for organizations aiming to boost their production capacities.
Welding Solution Choice Factors
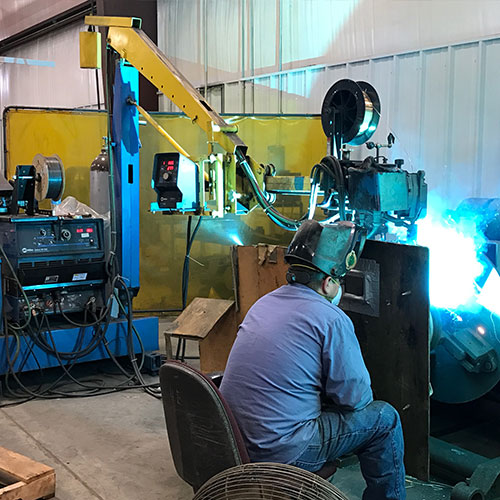
Another factor to take right into account is the dimension and intricacy of the parts being bonded. Some welding approaches are much better suited for intricate and small projects, while others are much more effective for larger and a lot more straightforward structures. In addition, useful reference take into consideration the speed and efficiency of the welding procedure. Relying on your manufacturing requirements, picking a welding solution that can meet your timeline and output needs is essential for preserving productivity. Ultimately, examine the cost-effectiveness of different welding services to ensure that you are getting the most effective worth for your financial investment. By very carefully considering these aspects, you can choose one of the most ideal welding service for your service needs.
Conclusion
In verdict, understanding the advantages of different kinds of welding services can considerably profit organizations in their decision-making procedure. MIG welding offers efficiency and speed, TIG welding offers high precision and clean welds, arc welding is affordable and functional, and spot welding is suitable for joining thin products. By taking into consideration these elements, services can pick one of the most ideal welding solution to fulfill their certain needs and demands.
MIG welding, additionally recognized as Gas Metal Arc Welding (GMAW), provides many advantages to businesses seeking effective and high-grade welding solutions. One of the crucial advantages of TIG Source welding is its versatility in welding various kinds of steels, including stainless steel, aluminum, copper, and exotic metals, offering services with an adaptable welding remedy for different projects.
Arc welding is recognized for its high welding rate, enabling reliable conclusion of welding tasks (Welding Inspection Service). Overall, the pros of arc welding make it a beneficial welding service for services looking for a flexible, affordable, and efficient welding option
MIG welding provides performance and speed, TIG welding provides high accuracy and tidy welds, arc welding is functional and cost-efficient, and area welding is optimal for joining slim materials.
Report this page